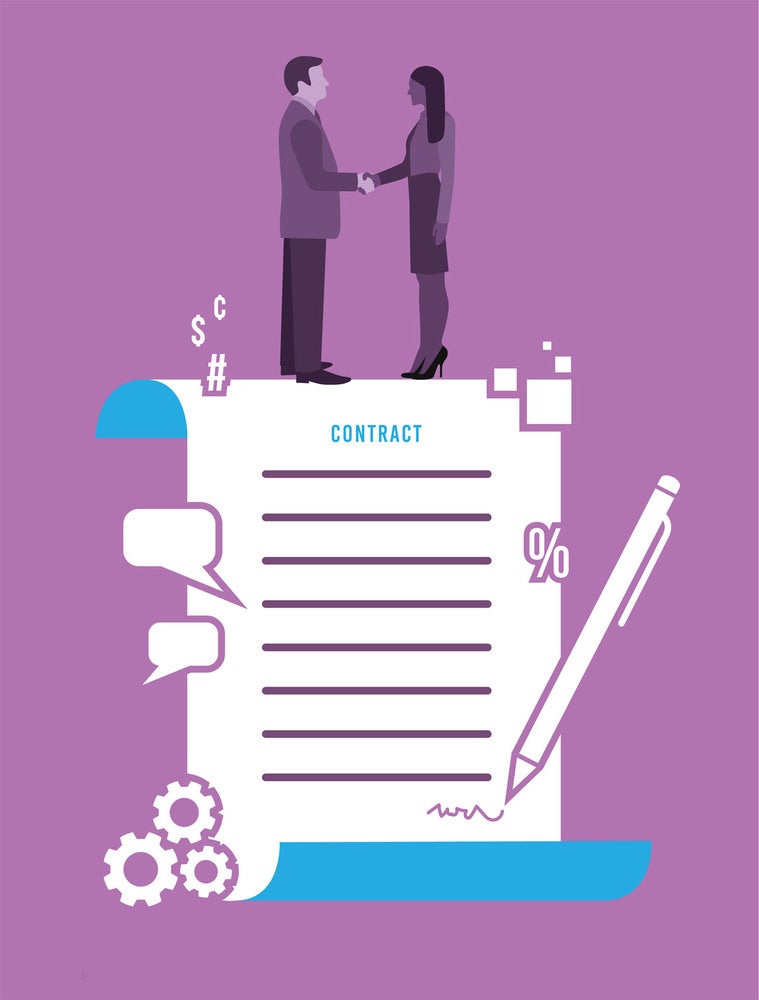
CHEAT SHEET
- EPC. The engineering, procurement, and construction (EPC) contract is the standard for power and energy construction projects. It can take many forms, and choosing the appropriate contract model and pricing structure is critical to project success.
- Contract model. The two basic contract model options for EPC contracts are “full wrap” or “turnkey” model, where the EPC contractor has full responsibility and delivers a finished product for the client, and the “partial wrap” model, where the contractor and owner split responsibility.
- Pricing model. After choosing a contract model, project participants will select a pricing model – and may choose different models for different project phases. There are many options, with the fixed price model and the target price model being the spectrum ends.
- Completion milestones. The contract’s completion milestone provisions should be drafted carefully as they manage the parties’ expectations on risk and responsibility and determine when the owner can begin operations.
All construction projects are inherently risky. Risk management and allocation among project participants is key to the success of any project. These issues are magnified in energy and power construction projects because they have long development and construction periods, are extremely capital intensive, and have other unique challenges, such as rapidly evolving technology, complex regulatory schemes, and changing end-user preferences stemming from the growing popularity of “green” power solutions. The project’s construction contract is one key opportunity for project participants to reduce and allocate risk by helping to document parties’ agreements and expectations regarding risk allocation.
The standard contract for power and energy construction projects is the engineering, procurement, and construction (EPC) contract. It takes many forms, and selecting the appropriate contract model and pricing structure to include in the EPC contract for each unique project is critical to a project’s success. In addition to these fundamental selections, an owner’s primary goal with any power and energy project is to generate power as soon as possible; and making that happen lies in key project completion milestones in any EPC contract: the mechanical, substantial, and final completion provisions.
The fundamental selections – Contract model and pricing structure
Project participants will need to select the most appropriate contract model for their project. The two basic options for EPC contracts are the “full wrap” or “turnkey” model and the “partial wrap model.”
The “full wrap” or “turnkey” model
In its classic form, the “full wrap” or “turnkey” model of the EPC contract establishes a one-stop-shop for the design and construction of the project. The EPC contractor is responsible for the engineering (design of the entire power plant), procurement (purchase, installation, and performance of all equipment), and construction of the entire project. Under a “full wrap” or “turnkey” model, the EPC contractor will fully provide all the detailed engineering designs of the project, procure all the equipment and materials necessary for the project, and then construct and deliver a functioning facility to their client. The EPC contractor is responsible from start to finish and delivers a finished product that simply requires the client to “turn the key” and begin operations.
An obvious benefit to an owner using this model is that the contractor assumes all responsibility and risks for major equipment. Project participants such as lenders and equity investors tend to like this model. In the event of a major equipment defect or failure, the buck stops with the EPC contractor and the owner will not expend extra resources pursuing multiple parties to determine responsibility. Another significant advantage of this model is that sharing of resources can lead to significant cost advantages. With all the work being completed under the umbrella of a single contract, major equipment can be shared (no need for repeating the expense of mobilizing and demobilizing cranes for individual tasks), as can manpower resources (the crew pouring concrete for a building or wiring the electrical for a system can be employed for other buildings and systems too).
But this model also presents drawbacks for an owner. A contractor who assumes all the responsibility and risks for major equipment will only do so in exchange for compensation. The overall cost of the project will increase as the contractor adds a risk premium to his fixed price.
The “partial wrap” model
In a “partial wrap” scenario, the EPC contractor does not have full responsibility for the entire project. Typically, the EPC contractor assumes the responsibility and risks for engineering and construction, but not for procuring the major equipment. The owner may purchase the major equipment and assign the purchase orders to the EPC contractor. Alternatively, the owner may already have the equipment in its possession. In either scenario, the EPC contractor is relieved of the obligation to procure the equipment and obtain the relevant equipment warranties but is still responsible for installing the equipment.
The partial wrap approach is best suited for owners who already have possession of major pieces of equipment or projects that require standard pieces of major equipment that can be procured less expensively by the owner directly. By relieving the contractor of the risk of procuring the equipment, the EPC contractor’s risk premium should decrease, resulting in a more favorable pricing model for the owner. On the other hand, if equipment malfunctions, the possibility of the EPC contractor and equipment supplier pointing fingers at each other rather than solving the problem as efficiently and economically as possible is a real risk for owners.
Having selected a contract model, project participants will next want to select an appropriate pricing model. Many pricing models can be selected for an EPC contract. At opposite ends of the spectrum are the fixed price model and the target price model, with a variety of other options available. It is also quite common for EPC contracts to utilize different pricing models for different phases of the project.
The fixed price model
The simplest approach is the fixed price model. In this type of contract, the EPC contractor agrees to perform the entire project for a fixed price.
The benefits of this model are obvious for an owner who gets the entire project for a determined price and costs set at the signing of the contract. However, owners should be wary of the fixed price model. This model is only appropriate where significant planning and engineering have been invested before the contract. Without a complete concept and detailed scope and specifications, a fixed price model is very risky for an owner. The owner must anticipate that in a fixed price model, the contractor will only provide exactly what is detailed in the contract. If unforeseen scope items or unknown environmental or plant conditions are discovered after contract signing, the contractor may seek a change order, which may both increase the cost and impact the project schedule as the contractor performs the additional work.
If the specifications are not painstakingly clear, an owner’s risk increases in a myriad of ways. The contractor will be incentivized to purchase the least expensive material and equipment that satisfy the specification requirements and potentially take shortcuts in the design, procurement, and construction processes to meet the timeline. All of this can have significant consequences on the quality of the project.
Target price model
The target price model is a cost-reimbursement model established through an open book estimate process. Typically, the contract cost is subject to a sharing mechanism. If the project is completed for below the pre-established “target price,” the contractor shares in the savings in the form of a bonus. And if the project is completed for more than the pre-established “target price,” the contractor shares in some portion of the final costs that exceed the target price.
Target pricing is a good option for fast-track projects because it does not require a fully defined concept and fully developed specifications at the time of contracting. However, the downside for an owner is the significant unknowns with respect to establishing the final contract price. This uncertainty may be unacceptable to other project participants such as equity investors and lenders. This model is only effective if there is a truly open book process that allows both the owner and contractor to realistically evaluate the potential costs of the project, as well as a fair and clearly defined sharing mechanism that fully incentivizes both parties to realistically project the final cost and time to complete the project.
Controlling project completion by drafting Completion Milestone Provisions
Completion milestones, usually called “mechanical completion” and “substantial completion,” are critical to managing and allocating risk around the project’s schedule. These terms help manage the parties’ expectations as to which party bears the risks and responsibilities relating to the plant at different stages of construction. The contract’s completion milestone provisions should be drafted carefully to ensure that the owner can begin to operate as soon as possible and to compensate the owner for lost revenues if construction delays occur, usually in the form of liquidated damages. It is imperative to keep in mind that the terms “mechanical completion” and “substantial completion” mean what the contract says they mean — and must be drafted with precision.
The first step is mechanical completion, which, in its most basic sense, means that the EPC contractor has installed all the equipment and it is operational. Some basic boilerplate requirements will go a long way to achieve mechanical completion. Consider, “The EPC contractor must perform the design, engineering, procurement permitting, construction, and installation of the equipment in accordance with the contract and manufacturers requirements and the contractor must complete the work necessary to cause the unit to operate safely.” But the devil is in the details, and it is important that all necessary mechanical and electrical needs of the specific project are contemplated and addressed in the contract as requirements for mechanical completion. No two projects are the same, and thus, no two mechanical completion contract provisions are the same. Lawyers drafting these provisions should work carefully with their engineering and construction colleagues to make sure the contract clearly addresses the particular requirements for each project.
No two projects are the same, and thus, no two mechanical completion contract provisions are the same. Lawyers drafting these provisions should work carefully with their engineering and construction colleagues to make sure the contract clearly addresses the particular requirements for each project.
The next step is substantial completion. Integral to establishing this completion milestone is performance testing. The EPC contractor should be responsible for performing testing to confirm that the equipment satisfies minimum performance guarantees, as well as to establish emissions and regulatory compliance.
Again, no two projects are the same and it is essential that all necessary performance testing needs of the specific project are proactively determined and documented when these provisions are drafted. Lawyers should work carefully with their engineering and construction colleagues to make sure these provisions address the project’s specific requirements. In addition, the substantial completion provision is the owner’s opportunity to set forth all the parameters needed from the EPC contractor before it is prepared to take over responsibility for operating the plant. This includes operations and maintenance (O&M) manuals, special tools, orientation and training, permits, licenses, and approvals. Finally, a requirement for substantial completion should always be that the owner and EPC contractor agree on a punch list for the project’s completion.
Substantial completion is the most important milestone because typically this is the stage that care, custody, and control of the project shifts from the EPC contractor to the owner. When this occurs, the risk of loss for the equipment and project shifts from the EPC contractor to the owner and, typically, this is the stage at which the owner can begin commercial operations. Again, the contract language is key, and the parties should specifically address in their milestone completion provisions what is required of the EPC contractor before care, custody, and control shift to the owner and before the owner begins commercial operations.
Eco-friendly contract management
Learn how environmental and corporate interests can align at ACC Docket’s website: accdocket.com/articles/green-contracts.cfm
Since a significant portion of the contract price is usually tied to achieving mechanical and substantial completion, these provisions help ensure the project is completed to the owner’s satisfaction. It is important that the owner draft the mechanical and substantial completion provisions so that the EPC contractor is required to deliver to the owner everything the owner needs to take over the project before achieving these milestones. At this stage, the EPC contractor’s performance is largely complete, most of the compensation has been earned, and the owner assumes the risk of the project. Therefore, it is advisable to include anything of importance to the owner as a requirement to achieving these deadlines.
Both interests can be satisfied by including a provision in the EPC contract to allow for early commercial operations. Typically, such a provision would allow the owner to begin operating individual units or the entire facility once power can be safely generated. By incorporating such a clause into an EPC contract, an owner can protect itself and ensure that technical requirements of mechanical completion and/or substantial completion do not unnecessarily prevent generating power as soon as practicable.
Other considerations
While this article focuses on the selection of the appropriate contract model and pricing structure and careful drafting of the completion milestones, the EPC contract should also include other additional key provisions to manage and allocate project risk. These include, for example, the EPC contractor’s standard of performance; project time and schedule; mechanical, substantial, and final completion; delay and performance liquidated damages; changes; limitation of liability; suspension, termination, and default; and disputes. Properly negotiating and documenting all of these specific contract terms is critical to a successful project. In any case, it is critical to remember that every project is different, and the details of each EPC contract must be carefully drafted to match your project.
ACC EXTRAS ON… Energy projects
Articles
Global Legal Insights - Energy 2019, 7th Edition (Nov. 2018).
Program Materials
Cool Tools for Power Rules: Modern Methods for Ensuring Compliance With Energy Regulations (Oct. 2016).
InfoPak
Construction and Projects Guide: Australia (March 2016).
ACC HAS MORE MATERIAL ON THIS SUBJECT ON OUR WEBSITE. VISIT WWW.ACC.COM, WHERE YOU CAN BROWSE OUR RESOURCES BY PRACTICE AREA OR SEARCH BY KEYWORD.